Can you weld with a plasma cutter? It’s a question many beginners in metalworking ask. I asked myself the same thing when I first started.
The short answer is no.
Many beginners try using plasma cutters for welding. This is a mistake. It wastes time and materials. Worse, it can cause serious problems. You could get burned, damage your tools, or ruin your project.
Plasma cutters are powerful tools. They are perfect for cutting through metal. They make clean cuts quickly. So, it’s easy to think, “If it can cut metal, it can weld it too.” I thought the same thing at first. But after trying it myself and learning more, I realized the truth. Plasma cutting and welding are not the same. They need different tools and skills.
In this guide, I’ll share what I’ve learned about plasma cutters. I’ll explain why they can’t weld and which tools work better for welding. I’ll also break down the science behind both processes and give you safety tips.
If you’ve ever wondered if a plasma cutter can weld, this guide will help. You’ll save time, avoid mistakes, and stay safe.
Let’s clear up this common myth so your projects are successful!
Why Can’t You Weld With a Plasma Cutter?
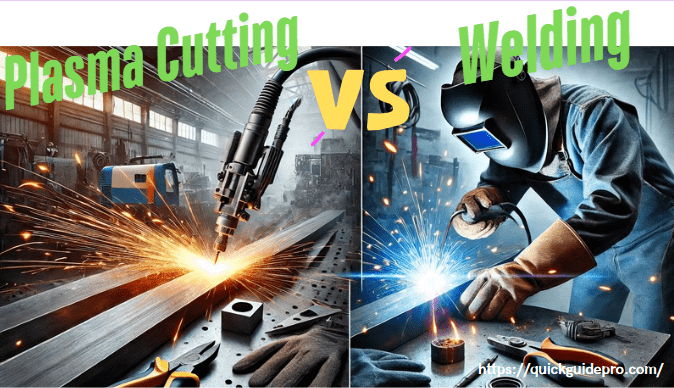
To understand why you can’t weld with a plasma cutter, it’s important to know how each tool works and what it’s designed to do.
Plasma Cutting vs. Welding: The Key Differences
Plasma cutting and welding are both processes that use heat, but they are used for different purposes. Plasma cutting is used to cut metal, while welding joins metal together.
Plasma Cutting: Plasma cutters use heat to melt metal and blow it away, creating a clean cut. They use a stream of ionized gas (plasma) that gets as hot as 30,000°F. This gas melts the metal and cuts through it. Plasma cutters are perfect for cutting metals like steel, aluminum, and brass. The heat is focused on a small area, allowing the tool to cut quickly and precisely. Learn more about how hot a plasma cutter gets and how it works in detail.
Welding: Welding, on the other hand, is used to join two or more pieces of metal. In welding, heat is applied to the metal to melt it, then the metal is fused together. Sometimes, filler material is added to make the bond stronger. Welding needs a different kind of heat. It must be spread over the whole joint to join the metals properly.
Plasma Cutting vs. Traditional Welding
Feature | Plasma Cutters | Traditional Welding (TIG, MIG, Stick) |
Role | Cutting | Joining |
Cost | Varies – often higher | Generally affordable |
Skill Level | Requires specific skills | Skills vary by method |
Quality of Finish | Precision cutting | Structurally strong joints |
Plasma Cutters Don’t Provide the Right Kind of Heat for Welding
Welding needs heat that is spread evenly across the metal joint. This heat must melt the edges of the metals and allow them to bond. Plasma cutters can’t do this. The heat from a plasma cutter is focused on a small area, which is great for cutting but not for welding.
In welding, the heat must be applied slowly and evenly to the entire joint. This way, the metals melt together smoothly and create a strong bond. Plasma cutters don’t have the control needed for this. They focus the heat in one place, which means they can’t spread it across a metal joint to weld the pieces together.
Plasma Cut Edges Are Not Smooth Enough for Welding
When you cut metal with a plasma cutter, the edges are often rough. This roughness can make it harder to weld. For welding to work well, the edges of the metal need to be clean and smooth. This helps the metal pieces fuse together properly.
The rough edges from a plasma cutter may need extra cleaning or grinding to make them ready for welding. Sometimes, the metal can be damaged or weakened by the plasma cutting process. This can make welding harder and may lead to a weak weld that could fail.
The Plasma Cutter’s Heat is Not Concentrated Enough for Welding
To weld, you need concentrated heat to melt the metal and join it. Plasma cutters create high heat, but it is focused in a small area, making it great for cutting but not welding. Welding requires a steady, controlled heat over a larger area to fuse the metals together.
Plasma cutters work by melting metal quickly in one place, which is fine for cutting but not for creating a strong weld. When welding, the heat must be spread out to ensure the metal joins properly. The plasma cutter simply doesn’t have the heat control or spread needed for welding.
Welding Needs Filler Material
Welding often requires filler material, such as a rod or wire, to fill gaps between the metals being joined. This material helps create a stronger bond. Plasma cutters don’t add filler material when cutting. This makes them unsuitable for welding, where the filler material is needed to reinforce the weld.
Welding also needs the right tools to feed the filler material into the joint. Plasma cutters can’t do this, so they can’t create the strong, lasting bond that welding is meant to achieve.
Plasma Cutting Can Damage the Material
Using a plasma cutter to weld can damage the metal. Plasma cutters work by applying a lot of heat to a small area, which can cause the metal to warp, crack, or distort. This is especially true if the metal is thin or sensitive to heat. When welding, the heat is applied more carefully, which reduces the risk of damage to the material.
Plasma cutters simply can’t give you the control needed to avoid this kind of damage. The heat they create can change the structure of the metal, making it harder to weld and leading to weaker welds.
Quick Facts:
- Plasma cutters are great tools for cutting metal, but they can’t be used for welding. They create focused heat that melts metal. This works for cutting but not for joining pieces together.
- The edges made by plasma cutters are often rough. These edges are not good for welding. Plasma cutters also don’t spread heat evenly, which is needed to join metal. Instead, the heat is too focused. This can even damage the material. Another problem is that plasma cutters don’t use filler material. Filler material helps make strong, lasting welds. Without it, the bond between metals may not hold.
- If you need to weld, you’ll need a MIG, TIG, or Stick welder. These tools give the steady heat and control needed for welding. Using the right tool will help you finish your project safely and with great results.
Frequently Asked Questions
Have more questions about plasma cutters and welding? Below are answers to the most common questions to help you understand these tools better.
Can You TIG Weld With a Plasma Cutter?
No, TIG welding requires different equipment with precise heat control and filler materials, which plasma cutters cannot provide.
Can You Weld Steel With a Plasma Cutter?
Plasma cutters are great for cutting steel, but they cannot weld it. Welding requires additional heat and filler material that plasma cutters do not offer.
Can You Cut Welded Metal With a Plasma Cutter?
Yes, plasma cutters can cut through welded metal, but they are better suited for cutting clean, unjoined surfaces.
Can You Weld Aluminum With a Plasma Cutter?
Plasma cutters can cut aluminum but cannot weld it. Welding aluminum requires specialized equipment like TIG or MIG welders.
Final Thoughts
For those asking “can I weld with a plasma cutter,” the answer is clear: these tools are designed for cutting, not welding.
Now that you know why plasma cutters can’t be used for welding, you can make better decisions when choosing the right tool for your metalworking tasks.
Whether you’re cutting or welding, each process requires its own specialized equipment. Success in metalworking comes from using each tool as intended and maintaining proper safety standards.
Understanding the differences will save you time, money, and frustration—and ensure your projects are safe and successful.
Ready to start your next metalworking project?
Make sure you have the right tools for the job! Explore more about plasma cutters and welding methods on our website to find the best equipment for your needs.
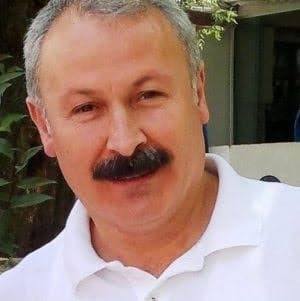
I’m Ivan D. Mitchell. I’m the Chief Engineer, Manufacturing Engineering Tool and Launch, specialising in automotive equipment design and build which meets World Class Manufacturing methodology. I have 15 years of work experience as a Tooling Specialist on some of the leading automotive manufacturing companies. When I launched this site, I wanted to create a platform where you’ll get everything about tools in one place. I also wanted to share my experience in the tool industry. I’ll do my best to share the information you need to truly make your tool using experience better. I hope you find our guides, reviews, information HELPFUL. If you have any inquiries, I’m always here to help you.