If you’re never done any plasma cutting before, you probably think that it just kind of pulls the trigger and away you go. But there are definitely some skills and plasma cutting tips and tricks to get the best results out of a plasma cutter.
We’re going to show you them today.
These tips are proven to be fruitful to increase efficiency, improve cut quality, and prolong the life of the consumables and the plasma cutter itself.
Take your time to read these tips. You’ll definitely be benefited from applying them.
30 Plasma Cutting Tips and Tricks to Make Your Cutting Project Awesome
Here are the tips.
1. Consider the following factors
There are many factors that affect plasma cutter cutting-quality on metal. These are:
• Type of plasma cutters
• Plasma cutting system
• Internal variables (e.g., cut height, cutting speed, choice of consumable)
• External variables (e.g., operator experience, gas purity, and material variability).
Hence, it’s essential to take into consideration these factors when attempting to improve the appearance of a cut.
2. Level the workpiece
Keep the torch at approximate 90-degree to the work surface. In other words, keep it square both from the side and front of the torch. Inspect if the material is warped or bent.
3. Practice before making the final cut
You should practice the cutting movements along your planned cutting path without pulling the trigger. Before starting a long cut, practice your actions. It’ll help to ensure that you have sufficient freedom of movement for making the continuous cuts.
4. Keep continuous contact with the work surface
When using a drag nozzle, keep continuous contact with the work surface. If you pause and then start the cut again at the same point, it may create irregularities in the cutting edge.
5. Keep a consistent travel speed
Always keep a constant travel speed and adjust cutting speed, as needed. Remember, cutting speed impacts dross levels. – Too fast cutting speed may create a splashback and top spatter. In this case, slow the cutting speed. Too slow speed may create excessive dross on the backside. In this case, increase your cutting rate.
6. To cut a straight line using a drag spacer and straight edge guide
a) Clamp the straight edge to the workpiece.
b) Keep torch at approximate 90-degree to work surface
7. Use personal plasma cutting table
You can’t effectively cut through metal when it is lying on top of a workbench or on your concrete floor. However, it’ll provide ample capability in a horizontal fashion if you use a plasma cutting table.
8. Follow the right cutting direction
Choose which technique works best for you- pull, push, drag left or drag right. However, most plasma cutter operators find the pull cutting direction comfortable rather than push it away.
9. Brace your cutting hand
Support your cutting hand with your non-cutting hand. This will help you to maintain a constant and steady cut by providing steadiness to your cutting hand. What’s more, it’ll allow you to maintain the optimal distance between the workpiece and the tip while cutting without a drag shield.
10. Use the right tip size for the right amperage setting
A lower amperage tip comes with a smaller orifice that helps to maintain a narrow plasma stream at the lower amp. setting. Using extended tips will help you reach out further for cutting while using patterns, in tight spaces, or corners. – At an 80-amp, if you use a 40-amp tip, it’ll distort the tip orifice and consequently reduce consumable life. – On the other hand, using an 80-amp tip on the lower amp will lead to a wider kerf as the tip won’t be able to focus the plasma stream.
11. Proper gas and constant flow
To get a good cut, you need consistent air pressure from your compressor. It also needs to be set precisely what the machine recommends. Additionally, inspect for any leaks or restrictions. And use proper size gas lines and regulators. It’s recommended to use high-quality, pure gas.
Take a look at our in-depth Primeweld Cut50 Air Inverter Plasma Cutter review.
12. Set the recommended voltage
Make sure the recommended voltage of the plasma cutter is set right. It’ll make your metal cutting tool work a lot better.
13. Before the final cut, make a sample cut first
It’s useful to make a sample cut on the same type of metal or material that you plan to cut. This will help you to ensure you’re using the right travel speed and amperage settings.
14. To cut the final edge of a thicker material…
On a thick workpiece, cutting the last little end is somewhat tricky. Roll the tip slightly towards the last little end of your work piece to achieve a clean-cut. You may also pause for a short time to completely break off the metal at the end of the cut.
15. To remove the dross easily….
Thick metals tend to leave dross on the bottom of the cut if you cut at your plasma cutter’s maximum output. However, by using a chipping hammer you can easily remove the dross.
16. Piercing thick and thin metals….
The backlash of the molten metal is responsible for quick degrading of the consumable’s life. Place the torch at about 45-degree in a direction away from your body for piercing thick metal. On the other hand, place the torch in a square position on the workpiece and pull the trigger for piercing thin materials.
17. For cutting bolt holes….
Plasma cutter is a handy machine for cutting bolt holes. It cuts bolt holes faster than a drill. First, penetrate or make a hole in the metal and then trace a small circle. A plasma cutter can penetrate metal up to one-half of its cutting thickness.
18. For cutting perfect circles…
It’s convenient to use circle guides for cutting varying sizes of circles. It’ll help you to cut perfect circles each time.
19. For cutting repeatable or specific shapes….
Using a template and tracing along the edge will make your cutting job of repeatable or specific shapes easy. While determining template size, take into consideration the cut width. Don’t forget to clamp the template to the base surface to resist the movement of the workpiece during cutting.
20. To cut a beveled edge….
Simply tilt the torch at a 30 to 40-degree angle and make the angled cut. It’s obvious that an inclined torch will cut an angled edge. Note that, bevel an edge is helpful to obtain 100% penetration on thicker materials.
21. Set the torch-to-work distance at the proper height
It’s convenient to use a drag shield if your machine is equipped with one. If the tip touches the work surface, it negatively affects the cut quality as well as consumable life. A drag shield helps you to rest the torch on the workpiece automatically maintaining a proper standoff for the torch tip** Maintaining a 1/8 or 1/16-inch standoff between the workpiece and tip while cutting will enhance the longevity of the plasma cutter consumables. Moreover, it helps to produce a cleaner cut and maximize the cutting capacity of the machine.
Alternative of drag-shield
Instead of drag shield, you can also use a roller guide to maintain a consistent standoff. It makes cutting a straight line with a handheld plasma cutter easy.
22. Blow the sparks AWAY
Always make sure you blow the sparks AWAY from you and other sensitive materials such as glass.
23. Inspect the consumables regularly
Worn consumables are responsible for inaccurate cut and arc starting problems. For this reason, you should inspect the consumables regularly for wear.
24. Clean the plasma cutter torch regularly
It’s essential to keep the internal and external torch threads clean and in good condition. Use electrical contact cleaner or hydrogen peroxide and a cotton swab to clean the torch.
25. Replace the electrode and nozzles at the same time
To ensure maximum cutting performance, replace the electrode and nozzles at the same time. Also, avoid over-lubricating O-rings.
** Make sure that you’re using the correct type of consumables. For this, verify the part numbers.
26. Replace the tip
When the tip of the electrode develops a pit or the tip hole becomes irregular and covered with spatter, it’s time to replace the tip.
** Electrode contains a small amount of hafnium (a highly conductive material). Each arc-start consumes hafnium.
27. Finger tighten the retaining cup
Never over-tighten the retain cap as the parts inside actually require to move to produce an arc. Only finger tighten the retaining cup.
28. Secure the ground clamp to clean metal
Only secure the ground clamp to clean metal for getting the best cutting performance. Grind off the paint or rust before clamping as these may inhibit the flow of electricity.
29. Place the ground clamp as close to the cut line
Try to place the ground clamp as close to the cut line as possible. If possible, place the clamp on the workpiece itself. Inspect the cables for loose connections, worn spots, or anything else that might resist the electrical flow.
30. Use edge start rather than pierce start
If the arc stretches to reach the metal, it’ll damage the consumable. Whenever possible, directly center the nozzle orifice over the edge of the workpiece and do the edge-start.
Conclusion
Using the right plasma cutting tips and tricks will you optimize your metal cutting, make the job easier, improve results, and increased productivity.
What’s more, applying these techniques will save countless hours that you may spend troubleshooting the plasma cutter before it goes on to the next step in the cutting process.
Not only that, it’ll enhance the consumable life and lower the plasma cutter operating costs at the same time.
Hence, try to apply these tips.
Your technique will certainly develop with practice!
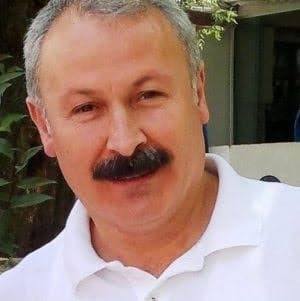
I’m Ivan D. Mitchell. I’m the Chief Engineer, Manufacturing Engineering Tool and Launch, specialising in automotive equipment design and build which meets World Class Manufacturing methodology. I have 15 years of work experience as a Tooling Specialist on some of the leading automotive manufacturing companies. When I launched this site, I wanted to create a platform where you’ll get everything about tools in one place. I also wanted to share my experience in the tool industry. I’ll do my best to share the information you need to truly make your tool using experience better. I hope you find our guides, reviews, information HELPFUL. If you have any inquiries, I’m always here to help you.
I didn’t know the torch needs to be at a level 90 degrees to work well. Recently, my sister has been looking into welding because she needs those services to develop certain projects she’s got. We’ll have to look into welding fabrication shop services.
This article is great inspiration for us!
Like!! I blog frequently and I really thank you for your content. The article has truly peaked my interest.