Have you ever used a plasma cutter and wondered, “Do you need gas for a plasma cutter, or can you just plug it in?” I had the same question when I first started cutting metal.
The answer? It depends.
The right setup can mean the difference between a smooth cut and a rough mess. After a few mistakes, I figured out what works. Let’s break it down so you get the best results—without the frustration!
Why Does a Plasma Cutter Need Gas?
Plasma cutters need gas to create plasma, cool the torch, and blow away molten metal for clean, precise cuts.
When I first started using a plasma cutter, I didn’t understand why gas was so important. Turns out, gas is the magic ingredient that makes the whole process work.
Here’s how it works: the gas (like compressed air, nitrogen, or oxygen) gets super heated and ionized, turning into plasma. This plasma is what melts through metal like butter.
But gas does more than just create plasma. It also cools the torch, preventing it from overheating. Plus, it blows away the molten metal, leaving you with a clean, smooth cut. I learned this the hard way when I tried cutting without enough gas—my cuts were jagged, and my torch got way too hot.
So, do you need gas for a plasma cutter? Absolutely. It’s not just an extra step—it’s the key to getting professional-quality results.
Do All Plasma Cutters Need Gas?
Not all plasma cutters need gas—some can run on compressed air, but gas is often required for better results, especially on thicker or specialty metals.
When I first started using plasma cutters, I thought all of them needed gas. Turns out, I was wrong.
There are two main types of plasma cutters: gas-based and air-based.
Gas-Based Plasma Cutters
These use gases like nitrogen, oxygen, or argon-hydrogen. They work best for industrial projects and cutting stainless steel or aluminum. I learned this the hard way when I tried cutting stainless steel with only compressed air. The cuts were rough, and my torch overheated. Switching to nitrogen changed everything.
Air-Based Plasma Cutters
These run on compressed air and are great for small projects and thin mild steel. I’ve used them for DIY tasks, and they work fine. But when I tried cutting thicker metal? Let’s just say the results weren’t pretty.
When Is Gas a Must?
If you’re working on industrial-grade projects or cutting materials like stainless steel or aluminum, gas is a must. I learned this the hard way when I tried cutting stainless steel with just compressed air. The cuts were rough, and the torch overheated. Switching to nitrogen made all the difference—cleaner cuts, less cleanup, and no overheating.
So, do all plasma cutters need gas? Not always. But if you want professional-quality results, especially for thicker or specialty metals, gas is your best friend.
What Gas Is Used for Plasma Cutting?
The type of gas you use matters. The most common gases for plasma cutting are compressed air, nitrogen, oxygen, and argon-hydrogen mixes. Each gas has its strengths, depending on the material and project.
When I first started plasma cutting, I thought all gases were the same. Boy, was I wrong! The type of gas you use can make or break your project.
Here’s a quick breakdown of the most common options and when to use them:
- Compressed Air: This is the go-to for beginners and hobbyists. It’s affordable, easy to find, and works well for cutting mild steel. I’ve used it for small DIY projects, and it gets the job done without breaking the bank.
- Nitrogen: If you’re cutting stainless steel or aluminum, nitrogen is your best friend. It gives you clean, smooth cuts and prevents oxidation. I switched to nitrogen for a stainless steel project, and the difference was night and day.
- Oxygen: For mild steel, oxygen is the MVP. It creates a clean edge and speeds up the cutting process. I used oxygen for a garage project, and the cuts were so clean, they barely needed finishing.
- Argon-Hydrogen Mix: This one’s for the pros. It’s perfect for thick stainless steel and aluminum. I tried it once for a heavy-duty project, and it sliced through the metal like butter.
Pro Tip
Always match the gas to your material. Using the wrong gas can lead to rough cuts, extra cleanup, and even damage to your torch.
How Much Gas Does a Plasma Cutter Use?
A plasma cutter’s gas usage depends on the cutter’s size, material thickness, and cutting speed.
- Smaller cutters use about 4-8 cubic feet per hour (CFH)
- Industrial models can use 20-40 CFH or more.
When I first started using a plasma cutter, I had no idea how much gas it would use. I quickly learned that gas consumption isn’t one-size-fits-all. It depends on your cutter’s size and what you’re cutting.
For example, my small 30-amp cutter uses about 6 CFH for thin metal sheets. But when I upgraded to a 60-amp cutter for thicker steel, the gas usage jumped to 15 CFH.
What Affects Gas Usage?
- Material Thickness: Thicker metal needs more gas to cut through. Cutting 1/4-inch steel uses less gas than 1-inch steel.
- Cutting Speed: Faster cutting speeds use more gas. Slow, precise cuts use less.
- Cutter Size: Bigger plasma cutters need more gas to power the plasma arc.
I remember working on a large project where I had to cut through 1/2-inch stainless steel sheets. My 40-amp cutter was struggling, and I was burning through gas like crazy. I switched to a 60-amp cutter with nitrogen, and the gas usage stabilized.
Lesson learned: match your cutter and gas to the job.
Real-Life Example: Last year, I worked on a custom metal gate project. I used a 50-amp cutter and nitrogen gas. Over two days, I went through two 80-cubic-foot gas bottles. At first, I thought that was a lot, but the clean, precise cuts made it worth it.
Pro Tip
Always check your cutter’s manual for gas usage guidelines. And keep an extra gas bottle on hand—running out mid-cut is a nightmare I don’t wish on anyone.
So, how much gas does a plasma cutter use? It varies, but with the right setup, you can manage it like a pro.
Best Gas for Plasma Cutting Different Metals
Choosing the right gas for plasma cutting can make all the difference in cut quality, speed, and torch lifespan. Let’s break down the best options for different metals.
Which Plasma Gas Gives the Best Results for Cutting Aluminum?
Nitrogen or an argon-hydrogen mix is best for cutting aluminum. They prevent oxidation and ensure clean, smooth cuts.
When I first tried cutting aluminum with compressed air, I was in for a rude awakening. The cuts were rough. Oxidation left behind an ugly, uneven edge. That’s when I learned aluminum needs special treatment.
Nitrogen is a great choice. It minimizes oxidation, leaving a smooth finish. If you’re cutting thick aluminum, an argon-hydrogen mix is even better. The hydrogen boosts cutting power, making it easier to slice through without overheating.
Pro Tip
Want that shiny, pro look on aluminum? Ditch the compressed air. Use nitrogen or an argon-hydrogen mix. Trust me—your cleanup time will be cut in half.
Which Plasma Gas Gives the Best Results for Cutting Stainless Steel?
Nitrogen or an argon-hydrogen mix works best for stainless steel. They keep it rust-free and deliver clean cuts.
I learned this the hard way when I used oxygen on stainless steel. Big mistake. The cuts looked fine at first, but over time, rust spots showed up. Oxygen reacts with stainless steel, ruining its corrosion resistance.
Switching to nitrogen was a game-changer. The cuts were sharp, clean, and rust-free. For thick stainless steel, an argon-hydrogen mix is even better. The hydrogen helps produce a smoother cut with less heat buildup.
Pro Tip
Cutting stainless steel? Want it rust-free? Stick with nitrogen or an argon-hydrogen mix. Your future self will thank you.
Which Plasma Gas Gives the Best Results for Cutting Mild Steel?
Oxygen is the best gas for cutting mild steel. It delivers fast, clean cuts with minimal slag.
I worked on a DIY metal gate using compressed air. The cuts were okay, but the edges were rough. I had to spend extra time grinding and cleaning. Then I switched to oxygen. Wow—what a difference! The cuts were so smooth I barely needed to touch them up.
Oxygen increases the cutting speed. It leaves a clean edge. It also creates a small amount of slag that flakes off easily, saving time on cleanup.
Pro Tip
Cutting mild steel? Want the fastest, cleanest cuts? Oxygen is your best bet. It makes the whole process smoother and more efficient.
Plasma Cutter Gas Bottle: What You Need to Know
Plasma cutter gas bottles come in many sizes. Small ones hold 20 cubic feet. Big ones hold 300 cubic feet. They have pressures from 2,000 to 3,000 PSI. Costs vary by size and gas type.
When I started using a plasma cutter, I didn’t think much about the gas bottle. I thought, “It’s just a tank of gas.” Wrong. The gas bottle you use affects your work, safety, and cuts.
Let’s break it down so you can choose well.
Types of Gas Bottles
Gas bottles come in sizes like 20, 80, and 300 cubic feet. Pressures range from 2,000 to 3,000 PSI.
I learned gas bottles aren’t one-size-fits-all. For small DIY jobs, a 20-cubic-foot bottle works. For big jobs, like cutting thick steel, you need a bigger tank—80 or 300 cubic feet.
Once, I ran out of gas mid-project. I was using a small bottle. It couldn’t keep up. Switching to an 80-cubic-foot tank helped. The cuts were smoother. I didn’t have to stop to refill.
Pro Tip
Check your plasma cutter’s manual for the right bottle size and pressure. Using the wrong size wastes time and gives bad cuts.
Safely Handling and Storing Gas Bottles
Store gas bottles upright. Secure them with chains or straps. Keep them in a cool, dry place. Keep them away from heat.
Safety is key with gas bottles. I learned this the hard way. I once knocked over a nitrogen bottle in my garage. Luckily, nothing happened. But it scared me.
Now, I always store bottles upright. I secure them with chains or straps. I keep them in a well-ventilated area. I keep them away from heat, like welding tools or sunlight.
Pro Tip
Buy a gas bottle cart. It makes moving heavy tanks easy. It cuts the risk of accidents. Your back will thank you.
Cost Considerations and Where to Buy or Refill
Gas bottles cost 20 to 200. Size and gas type change the price. Refills are cheaper. Get them at welding supply stores or gas distributors.
When I started, I was shocked by gas bottle costs.
- A small 20-cubic-foot bottle of nitrogen cost 50.
- A big 300−cubic−foot tank cost over 50.
- A big 300−cubic−foot tank cost over 200.
But refills are cheaper.
I refill my bottles at a local welding supply store. It’s easy. The staff knows their stuff. If you’re on a budget, rent a bottle instead of buying one.
Pro Tip
Call around to compare prices. Some places give discounts for regular customers or bulk refills. It’s worth the effort to save money.
Can You Use a Plasma Cutter Without Gas?
You can try, but it won’t work well. Gas is key for clean cuts and keeping your torch safe.
When I started using a plasma cutter, I thought gas was optional. I was wrong. Gas is not just helpful—it’s necessary.
What Happens If You Run a Plasma Cutter Without Gas?
No gas means bad cuts, a hot torch, and possible damage.
I once tried cutting metal without gas. It was a mess. The cuts were rough. The torch got too hot. I had to stop to avoid breaking it.
Gas does three big things:
- Makes Plasma: Gas turns into plasma to cut metal.
- Cools the Torch: No gas means the torch overheats.
- Clears Molten Metal: Gas blows away melted metal for clean cuts.
Pro Tip: Never skip the gas. It’s like running a car without oil. It won’t end well.
A Cautionary Tale: The Time I Tried Cutting Without Gas
I ruined my project and almost broke my cutter.
Here’s what happened. I ran out of gas mid-project. Instead of stopping, I kept going. The cuts were awful. I spent hours fixing them. My torch started acting up. It cost me time and money.
Lesson learned: Always use gas. It’s not worth the risk.
When Can You Get Away Without Gas?
Almost never. Even thin metal needs gas for good cuts.
Some people use compressed air in emergencies. It works for thin metal but not well. For anything thicker, you need the right gas.
Pro Tip: Keep extra gas on hand. Running out mid-cut is frustrating.
Gas is a must for plasma cutting. Skipping it leads to bad cuts and broken tools.
If you’re new to plasma cutting, don’t skip the gas. Use the right gas for your project. Nitrogen for stainless steel. Oxygen for mild steel. Argon-hydrogen for aluminum.
So, can you use a plasma cutter without gas? Yes, but you shouldn’t. Your cuts and tools will thank you.
Plasma Cutting with Air vs. Gas
Compressed air works for thin mild steel. Specialized gases like nitrogen or oxygen are better for thicker or specialty metals like stainless steel and aluminum.

When I started plasma cutting, I used compressed air. It was cheap and easy. It worked fine for thin mild steel. I used it for small DIY projects like metal signs or fixing tools. But when I tried cutting stainless steel or thicker metals, it didn’t work well. The cuts were rough. My torch got too hot. That’s when I learned about specialized gases. Gases like nitrogen, oxygen, and argon-hydrogen are much better for tough jobs. Nitrogen stops rust on stainless steel and aluminum. Oxygen cuts mild steel fast. Argon-hydrogen handles thick metals with ease.
So, when should you use air or gas?
Use compressed air for thin mild steel (under 1/4 inch) and small jobs. It’s great for beginners. But for thicker metals, stainless steel, or aluminum, you need specialized gases. I learned this the hard way. I tried cutting stainless steel with air, and it was a mess. Switching to nitrogen saved the project. The cuts were clean and smooth.
In the end, compressed air is good for beginners. But specialized gases are key for pro-level results. Whether you’re doing a DIY project or a big job, pick the right option. It makes all the difference.
**Pro Tip:** Match your gas to the material. Keep both options ready. Use air for small tasks. Use gas for bigger, tougher jobs.
Compressed Air vs. Specialized Gas
Feature | Compressed Air | Specialized Gas |
Cost | Low – just need an air compressor | High – needs gas tanks and refills |
Best for | Mild steel, thin metal, DIY jobs | Stainless steel, aluminum, thick metal |
Cut Quality | Decent, but rougher edges | Smoother, cleaner cuts |
Oxidation Risk | High – can cause rust | Low – prevents oxidation |
Torch Cooling | Less effective – can overheat | Better cooling – lasts longer |
Convenience | Easy – no extra setup | Needs regulators and gas types |
FAQs About Plasma Cutter Gas
Here are answers to some common questions about gases used in the plasma cutting process.
What is the cheapest gas for plasma cutting?
The cheapest gas is usually compressed air. It’s easy to get and works well for thin materials or small projects. It’s a good choice for DIYers who need to save money.
Do I need an air compressor for a plasma cutter?
Yes, if your plasma cutter uses compressed air. You’ll need an air compressor to provide the pressure. Many plasma cutters for small or DIY projects use air-based systems, so an air compressor is required.
Can I use CO₂ for plasma cutting?
No, CO₂ is not a good choice for plasma cutting. The best gases for this are oxygen, nitrogen, and compressed air. CO₂ won’t create the right conditions for clean cuts.
Which gas is best for industrial plasma cutting?
Nitrogen is the best gas for industrial plasma cutting. It’s great for cutting thicker metals like stainless steel and aluminum. It provides clean cuts and stops oxidation, making it perfect for industrial work.
Final Thoughts
Plasma cutting is one of those skills where the little details matter. Choosing the right gas is one of the biggest details. Whether you’re a beginner working on a DIY project or a pro handling tough materials, the gas you use can make all the difference. It can turn a rough, messy cut into a smooth, clean one.
Before you start your plasma cutter, take a moment to pick the right gas for your material. Your cuts—and your stress level—will thank you.
Got more questions about plasma cutters? Leave them in the comments below! I’d love to help and share more tips from my own journey.
Happy cutting!
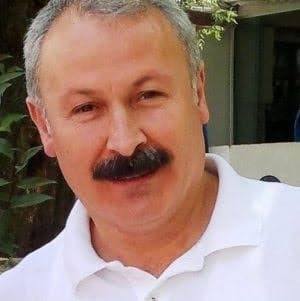
I’m Ivan D. Mitchell. I’m the Chief Engineer, Manufacturing Engineering Tool and Launch, specialising in automotive equipment design and build which meets World Class Manufacturing methodology. I have 15 years of work experience as a Tooling Specialist on some of the leading automotive manufacturing companies. When I launched this site, I wanted to create a platform where you’ll get everything about tools in one place. I also wanted to share my experience in the tool industry. I’ll do my best to share the information you need to truly make your tool using experience better. I hope you find our guides, reviews, information HELPFUL. If you have any inquiries, I’m always here to help you.