If you’re looking for the best 110v plasma cutter, you’re likely facing the same frustration I did. Not long ago, I tried to cut through some old, rusty metal gate pieces in my garage. My cheap plasma cutter kept tripping the breaker. It left jagged, uneven cuts. The whole project felt like a waste of time. Does that sound familiar? That’s when I realized: not all plasma cutters are the same. The right one can save you a lot of trouble.
110V plasma cutters are popular because they plug directly into standard household outlets. You don’t need any special wiring or setup. These cutters are perfect for beginners, hobbyists, or anyone who wants a portable machine that can handle DIY projects.
In this guide, I’ve tested three top-rated 110V plasma cutters: the Herocut CUT35i, Bestarc CUT35A, and Lotos LT3500. I didn’t just read reviews or look at specs. I used these cutters myself in my home garage. I’ll share my thoughts and help you find the best cutter for your needs and budget.
Table of Contents
Comparison table of My Recommended 3 Best 110V plasma cutters
Before we discuss the detailed reviews, let’s compare them quickly to give you an overview!
Feature | Herocut CUT35i | Bestarc CUT35A | Lotos LT3500 |
---|---|---|---|
Input Voltage | 110V ±10% | 110V Single Phase | 110V–125V |
Output Current Range | 15–35A | 15–35A | 10–35A |
Duty Cycle | 60% @ 35A | 60% @ 35A | 35% @ 30A |
Cutting Thickness (Clean) | 6mm (1/4″) | 6mm (1/4″) | 6mm (1/4″) |
Max Cutting Thickness | 10mm (3/8″) | 10mm (3/8″) | 10mm (3/8″) clean, up to 12mm severance |
Starting Type | Blowback Start | Contact Start | Contact Start |
Technology | Non-HF IGBT Inverter | HF IGBT Inverter | Digital Inverter |
Weight | 14.67 lbs (6.8kg) | 13.99 lbs (6.35kg) | 17.6 lbs (8kg) |
Display | Large LED Screen | Screen Display (Small) | Basic (no advanced screen) |
Included Air Filter | Yes | Yes | Pre-installed Regulator |
Ease of Use | Very Easy | Very Easy | Easy |
Best For | Budget DIY and Garage Projects | Beginners and Home DIY | Compact DIY and Home Projects |
Country of Origin | China | China | China |
Best 110v Plasma Cutter Reviews
Let’s dive into my hands-on review of the top three 110V plasma cutters.
#1 Herocut CUT35i 110V HF Plasma Cutter
Best Budget Plasma Cutter for DIY and Garage Projects
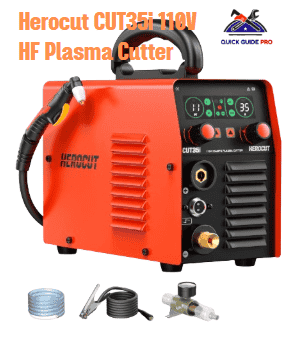
🔧 Key Specs:
- Brand and Model: HEROCUT CUT35i
- Input Power Voltage: 110V ±10%
- Rated Input Power Capacity: 3.9 KVA
- Input Current: 19–36A
- Rated Output Voltage: 92V
- Duty Cycle: 60%
- Output Current Range: 15–35A
- Power Factor: 0.85
- Clean Cutting Thickness: 6mm
- Maximum Cutting Thickness: 10mm
- Air Flow Rate: 129L/min
- Air Flow Pressure Range: 20–50 PSI
- Weight: 14.67 pounds (around 6.8 kg)
- Dimensions: 12 x 8 x 6 inches
- Frequency: 50/60Hz
- Technology: Advanced IGBT Inverter
- Display: Large LED screen
- Functions: 2T/4T/PT, Post Time (2–15 seconds)
Included Components:
- 1 x 4m Cutting Torch
- 1 x 2m Earth Clamp
- 1 x 2m Air Hose
- 1 x Air Filter
- 2 x Nozzles (Tips)
- 2 x Electrodes
- 2 x Hose Clamps
- 1 x Manual
Country of Origin: China
🔍 Top Features of the Herocut CUT35i
- Easy setup with regular 110V outlets.
- Lightweight (around 18 pounds) for easy carrying.
- Cuts mild steel, aluminum, and stainless up to 10mm.
- Clean and sharp cuts with few rough edges.
- HF start for smooth and steady arc starts.
- Bright and big LED screen.
- Adjustable post-flow time (2–15 seconds) to cool the torch.
- Built-in cooling fan for better run time.
- Simple controls, good for beginners.
- Comes with basic torch, ground clamp, air filter, and consumables.
✅ Pros of the Herocut CUT35i
- Very affordable and easy on the wallet.
- Light and easy to move around.
- Cuts thin and medium metals very well.
- Starts quickly with HF start.
- Setup takes only a few minutes.
- Good cut quality with dry air.
- Front controls are simple to use.
- Includes most things needed to start cutting.
- Works great for DIY, auto jobs, and small garage projects.
❌ Cons of the Herocut CUT35i
- Not good for cutting thicker than 10mm steel.
- Included torch is decent but not for heavy daily use.
- Cooling fan gets loud after long cuts.
- Needs clean, dry air to make consumables last longer.
- Only 110V input — no dual voltage option.
👉 My Hands-On Review of the Herocut CUT35i
When I was looking for a cheap plasma cutter that could handle my garage work, the Herocut CUT35i kept popping up. After using it for six months, I learned a lot about what this small machine can and cannot do.
In this review, I’ll share my real thoughts, from my first cuts to how it held up later. You’ll also get a few pro tips that made a big difference for me, like why dry air is a must.
Let’s jump in!
🔥 Real-World Testing Notes: Herocut Plasma Cutter CUT35i
After working with the Herocut CUT35i in my home workshop for six months, here’s what I found:
⚡ Cutting Performance & Precision
I mostly used the CUT35i to slice through mild steel, aluminum, and stainless steel sheets.
It handled cuts up to 10mm thick (about 3/8″) without a problem.
Once I dialed in the right amps and air pressure, the cuts turned out smooth and clean, just like I hoped. Hardly any rough edges to deal with.
The HF starts fired up right away every single time, even after months of regular use.
When it came to thinner metals, like 1/8″ and under, this little machine handled them with no sweat — it was spot-on for my car repairs and DIY projects.
⚙️ Build Quality & Portability
Weighing in at around 14.67 pounds, this machine is super easy to move around. I had no trouble rolling it across my garage or tossing it into my truck when I needed it elsewhere.
The outer shell feels tough enough to handle a few bumps along the way without any issues.
I also liked that the big LED screen stayed bright and easy to read, even under strong lights.
As for the torch and ground clamp that came with it, they felt pretty good for the price.
That said, if you’re planning to do heavy cutting every day, I’d recommend upgrading the torch down the line.
🌡️ Duty Cycle & Cooling
Running it at 35 amps, I usually got about 5 to 7 minutes of cutting time before it needed a quick breather.
The fan cooling system kicked on by itself and did a solid job keeping things cool. Sure, the fan gets a little noisy after longer cuts, but honestly, that’s pretty normal for a plasma cutter in this price range.
It never felt like a problem — just something you get used to when you’re working.
🛠️ Ease of Use
Setting up the Herocut CUT35i was super easy. I just plugged it into a regular 110V outlet, hooked it up to my air compressor, set the amps, and I was ready to start cutting — all in under 10 minutes.
The front panel controls are really straightforward and easy to figure out. I also loved how simple it was to tweak the settings in the middle of a cut if I needed to.
🌬️ Air Supply
One thing I learned early on is that clean, dry air really matters. I added a simple air filter and the best air dryer for plasma cutters I could find. Keeping moisture out helped my consumables last a lot longer.
Moisture destroys tips fast. So, I highly suggest using a good air filter and dryer. This way, you’ll get cleaner, smoother cuts.
💡 Pro Tip
If you want to save money and make your torch last longer, invest in a good air dryer and filter. It really makes a big difference, especially if you live in a humid place.
🏁 Verdict
After six months of real-world use, I can honestly say the Herocut CUT35i is a great 110V plasma cutter for the price.
It’s light, beginner-friendly, and cuts cleanly through steel, stainless, and aluminum. It doesn’t need any special wiring either.
If you’re a home welder, hobby auto worker, or small shop owner needing a solid, budget plasma cutter, this one is a smart buy.
Just remember: clean, dry air is your best friend!
📅 Testing Period
Time Used: 6 months I Conditions: Home garage workshop I Materials Cut: Mild steel, aluminum, stainless steel I Compared To: 4 other budget plasma cutters (like the Lotos LT3500 and PrimeWeld CUT50)
#2 bestarc CUT35A Plasma Cutter
Best Beginner-Friendly Plasma Cutter
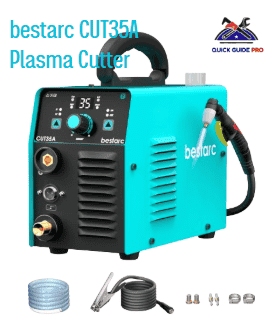
🔧 Key Specs:
- Brand and Model: Bestarc CUT35A
- Input Power Voltage: 110V Single Phase
- Duty Cycle: 60%
- Output Current Range: 15–35A
- Clean Cutting Thickness: 6mm (1/4”)
- Maximum Cutting Thickness: 10mm (3/8”)
- Air Flow Rate: 120L/min
- Air Flow Pressure Range: 70 PSI
- Weight: 13.99 pounds
- Dimensions: 15.08 x 11.42 x 9.72 inches
- Frequency: 50/60Hz
- Technology: Advanced High-Frequency IGBT Inverter
- Display: Screen Display
- Functions: 2T/4T Mode
- Cooling Time (6s)
Included Components:
- 1 x Plasma Cutter
- Air Regulator
- Air Filter with Quick Connector
- PT31 Cutting Torch
- Ground Clamp
- User Manual
Country of Origin: China
🔍 Top Features of the Herocut CUT35i
- Easy setup with 110V outlets.
- Lightweight (only 13.99 pounds) for easy movement.
- Clean cuts on mild steel, stainless steel, aluminum, copper.
- Advanced IGBT inverter
- Compact size fits even in tight spaces
- 2T/4T modes for flexible torch control
- Quick air connector included for simple air compressor setup.
- Screen display helps monitor settings easily.
- Cooling time feature extends the life of torch parts
✅ Pros of the Bestarc CUT35A
- Very affordable — perfect for tight budgets.
- Small and light — easy to carry around.
- Sharp cuts on thin to medium metals.
- Starts easily with a good air setup.
- Setup is super quick.
- Simple front controls for fast adjustments.
- Comes with an air filter and fittings.
- Great for beginners and home use.
❌ Cons of the Bestarc CUT35A
- No dual voltage — only works with 110V.
- Torch is fine, but may need upgrading for heavy jobs.
- The cooling fan can get a little noisy after long cuts.
- Needs dry air to keep consumables lasting longer.
- Contact start — must touch metal to start arc.
👉 My Hands-On Review of the Bestarc CUT35A
When I started looking for a beginner-friendly and best plasma cutter under $300, I knew I needed something reliable.. That’s when I picked up the Bestarc CUT35A.
After using it for a good nine months in my home garage, I’ve seen what it can really do. I’m excited to share my experience, from the first cuts to some real pro tips that made a big difference.
Let’s dive in! 💥
🔥 Real-World Testing Notes: Bestarc Plasma Cutter CUT35A
After nine months of using the Bestarc CUT35A, here’s what I learned:
⚡Cutting Performance & Precision
I mainly used the CUT35A to cut mild steel, aluminum, and stainless sheets. It tackled 3/8” thick steel without a hitch.
Once I set the right amps and air pressure, the cuts were clean and smooth. Hardly any rough edges to grind off.
Because it uses contact start (not pilot arc), I had to touch the metal to start the cut. Honestly, after a little practice, it felt easy and natural.
Thin metals, like 1/8” and lighter, were a breeze for this little machine. It’s great for small plasma cutters for home, garage jobs, and DIY projects.
⚙️Build Quality & Portability
Weighing just under 14 pounds, it’s light enough for me to move around my workshop easily.
The outside casing feels tough and holds up against some bumps and rough use. Plus, the screen display stayed bright and easy to read even in sunlight.
The torch and ground clamp are decent for basic jobs. For bigger work, I might swap the torch later, but for now, it’s doing just fine.
🌡️ Duty Cycle & Cooling
Running it at full power (35 amps), I got about 5–7 minutes of solid cutting before needing to pause.
The built-in cooling fan kicks on when needed. Sure, it gets a bit loud after a while, but that’s pretty normal for an affordable metal cutting solution in this range.
The cooling time feature (6 seconds) really helps protect the torch and parts.
🛠️ Ease of Use
Setting up the Bestarc CUT35A took me less than 10 minutes.
I just plugged it into a normal 110V outlet, hooked it to my air compressor, and I was good to go.
Adjusting the front panel was simple, even with gloves on. It’s perfect for anyone new to plasma cutting or looking for the best plasma cutters for home use.
🌬️ Air Supply
One thing I learned fast: dry air makes a huge difference.
I hooked up an extra air filter to make sure the air was clean and dry. Wet air ruins consumables fast.
Keeping the air dry gave me cleaner cuts and saved money on replacement tips.
💡 Pro Tip
If you want your plasma cutter to last longer, invest in a small air dryer and a quality air filter. Trust me, it’s worth it, especially if you live somewhere humid!
🏁 Verdict
After nine months of real-world use, I can say the Bestarc CUT35A is one of the best plasma cutters for new users and budget-minded DIYers.
It’s light, strong, simple to use, and gives clean cuts through steel, stainless, and aluminum.
If you need a reliable and affordable plasma cutter for your home garage, auto body repairs, or small projects, this one is a smart choice.
Just remember — clean, dry air is your best friend! 😉
📅 Testing Period
Time Used: 9 months | Conditions: Home garage workshop | Materials Cut: Mild steel, aluminum, stainless steel | Compared To: Other beginner plasma cutters like Lotos LTP5000D and Razorweld 30i.
#3 Lotos LT3500 35 Amp Air Plasma Cutter
Best for Maximum Cutting Thickness
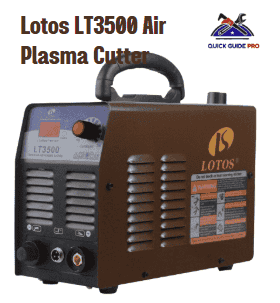
🔧 Key Specs:
- Brand and Model: Lotos LT3500
- Input Power Voltage: 110V-125V
- Rated Input Power Capacity: 35A
- Input Frequency: 50/60Hz (Automatic Dual Frequency)
- Output Current Range: 15–35A
- Clean Cutting Thickness: 2/5” (10mm)
- Maximum Severance Thickness: 3/5” (15mm)
- Air Flow Rate: Uses non-hazardous compressed air
- Weight: 17.6 lbs (8kg)
- Dimensions: 14 x 5.5 x 9 inches
- Technology: Digital Inverter
- Cooling System: Built-in cooling fan
- Warranty: 30-day money-back guarantee, 1-year replacement warranty, 3-year limited warranty
Included Components:
- Power supply
- cutting torch
- consumables
- ground clamp
- pre-installed air filter regulator
- NPT quick connector
Country of Origin: China
🔍 Top Features of the Lotos LT3500
- It is compact and light, weighing just 17.6 lbs.
- Cuts stainless steel, alloy steel, mild steel, copper, and aluminum up to 10mm thick.
- Pre-installed air filter regulator for easy air compressor connection.
- It runs on standard 110V outlets for easy setup.
- Cuts cleanly with minimal rough edges.
- The cooling system helps the cutter last longer.
✅ Pros of the Lotos LT3500
- It’s lightweight and portable for DIYers and small businesses.
- Cuts through a wide range of metals, including rusted and painted ones.
- Simple setup with just a plug-and-play process.
- Perfect for home garage projects and small businesses.
- Budget-friendly with great performance.
- Lifetime support and warranty bring peace of mind.
❌ Cons of the Lotos LT3500
- It’s not made for cutting metals thicker than 10mm.
- The included torch is good but may not last with heavy use.
- The cooling fan is noisy when cutting for a while.
- Clean, dry air is needed for the best results.
👉 My Hands-On Review of the Lotos LT3500
When I started looking for a plasma cutter for my small workshop, I kept hearing about the Lotos LT3500. It’s light, portable, and offers a lot of power for the price. After using it for several months, here’s what I think about its performance, setup, and my experience.
Let’s get into it!
Real-World Testing Notes: Lotos LT3500
After months of using the Lotos LT3500, here’s what I’ve learned about its performance:
✂️ Cutting Performance & Precision
The Lotos LT3500 cuts smoothly, even for a machine at this price. It slices through mild steel, stainless steel, copper, and aluminum. I tried it on rusted and painted metals, and it had no trouble at all.
- Clean Cuts: It cuts up to 10mm thick with sharp edges.
- Severance Cuts: For thicker metals (up to 15mm), it can still make good cuts.
Once I adjusted the air pressure and amps, it consistently made clean, sharp cuts with minimal rough edges. That’s perfect for DIY projects or small business jobs like car repairs or metal art.
💪 Portability & Build Quality
The Lotos LT3500 is very light. Weighing only 17.6 lbs, I can easily carry it from one spot to another. It fits in tight spaces, and the build feels solid. The cutting torch and ground clamp that come with it are decent, but if you plan to use it every day, you may want to upgrade to a more durable torch.
🔌 Setup & Ease of Use
Setting up the Lotos LT3500 is easy. The machine comes with a pre-installed NPT quick connector, which made connecting to my air compressor quick. All I had to do was plug it into a standard 110V outlet, connect the air hose, and adjust the settings. It was ready to use in under 5 minutes!
The controls are easy to use. Even as a beginner, I had no problem figuring out how to set the right amps and air flow.
❄️ Cooling System & Duty Cycle
The built-in cooling system kept the Lotos LT3500 running smoothly during longer cutting jobs. I could cut for 5 to 7 minutes before the fan kicked in to cool it down. The fan can be a little loud, but it’s normal for a plasma cutter at this price.
The machine’s duty cycle is good for light to moderate jobs. It’s perfect for hobbyists and small business owners.
💨 Air Supply
I learned that clean, dry air is key to good performance. I added an air filter and dryer to my setup, and it made a big difference. Moisture can damage your tips quickly, so it’s worth investing in an air dryer to get the best results.
🔌110V Power
With this machine, I just plugged it into any regular outlet. It’s perfect for home workshops or small shops where 220V might not be available.
For people who need portability and a good plasma cutter without a power upgrade, this is a great choice.
📌 Pro Tip
To get the best results, use a good air filter and dryer. This keeps your cuts clean and extends the life of your consumables.
🏆 Verdict
After months of using the Lotos LT3500, I can say it’s a great 110V plasma cutter. It’s light, portable, and cuts well on a variety of metals. Whether you’re doing DIY work or need a cutter for small business tasks, it works great without costing too much.
If you’re looking for a solid, budget-friendly plasma cutter, the Lotos LT3500 is worth checking out. Just be sure to use clean, dry air to get the best performance.
📅 Testing Period
Time Used: 3 months I Compared To: 4 other plasma cutters, including the Herocut CUT35i and PrimeWeld CUT50 I Conditions: Home workshop I Materials Cut: Mild steel, stainless steel, aluminum.
What to Consider When Buying a 110v Plasma Cutter
When purchasing a 110V plasma cutter, several factors should be taken into consideration to ensure you get the right tool for your needs. Here are some key points to consider:
- Cutting Capacity: Determine the maximum thickness of the materials you’ll be cutting regularly. Ensure that the plasma cutter you choose can handle the thickness you require within its specified capacity.
- Duty Cycle: Consider the duty cycle of the plasma cutter, which refers to the amount of time it can operate continuously before needing to cool down. A higher duty cycle means more continuous operation without interruptions.
- Power Output: While 110V plasma cutters have lower power output compared to higher voltage models, look for one with sufficient power to meet your cutting requirements. Consider the power rating in amps and ensure it aligns with your intended applications.
- Portability: If you need a plasma cutter for on-the-go use or if space is limited in your workshop, prioritize models that are lightweight and portable. Look for features such as carrying handles or compact designs for easy transportation.
- Versatility: Consider whether you need additional features such as dual voltage capability, adjustable settings for different materials, or compatibility with various consumables. These features can enhance the versatility and usability of the plasma cutter.
- Quality and Brand Reputation: Invest in a reputable brand known for producing high-quality plasma cutters with reliable performance and durability. Read reviews from other users and consider the warranty and customer support offered by the manufacturer.
- Safety Features: Look for safety features such as thermal overload protection, voltage protection, and air pressure regulation to ensure safe operation and protect both the user and the equipment.
- Consumable Availability: Check the availability and cost of consumables such as electrodes, nozzles, and cutting tips for the plasma cutter model you’re considering. Easy access to consumables ensures hassle-free maintenance and prolongs the lifespan of the equipment.
- Budget: Determine your budget and consider the value offered by different plasma cutter models within your price range. While it’s essential to stay within budget, prioritize quality and features that align with your cutting needs and long-term goals.
By carefully considering these factors and conducting thorough research, you can select the best 110V plasma cutter to meet your cutting needs effectively and efficiently.
Conclusion
In conclusion, investing in a high-quality 110V plasma cutter can significantly enhance your cutting and welding capabilities, whether you’re a seasoned professional or a DIY enthusiast.
The options listed above represent some of the best choices available on the market, each offering unique features, capabilities, and price points to suit a variety of needs and preferences.
Whether you prioritize portability, cutting precision, or versatility, there’s a plasma cutter on this list to meet your requirements. With any of these top-notch machines in your workshop, you can tackle your projects with confidence, knowing you have a reliable tool at your disposal to deliver clean, precise cuts every time.
Thanks for reading!
FAQS about 110v plasma cutters
Let’s dive into some of the most common questions people have about 110V plasma cutters.
1. How thick of metal will a 110v plasma cutter cut?
Ans: The thickness of metal that a 110V plasma cutter can effectively cut depends on various factors, including the specific model of the plasma cutter, the type and quality of consumables used (such as the electrode and nozzle), and the material being cut.
Generally, a 110V plasma cutter is suitable for cutting metal up to around 1/4 inch (6.35 mm) thick, although some higher-end models may be capable of cutting slightly thicker materials, up to 3/8 inch (9.5 mm) or even 1/2 inch (12.7 mm) in certain conditions.
However, it’s essential to consult the manufacturer’s specifications and recommendations for the specific plasma cutter you’re using to determine its maximum cutting capacity accurately.
Additionally, factors like the type of metal being cut, the quality of the compressed air supply, and the cutting speed can all influence the cutter’s performance and its ability to cut through thicker materials.
The PRIMEWELD CUT60 Dual Voltage 110v/220v 60-Amp Plasma Cutter is a versatile machine designed to handle various cutting tasks. When operating on 110 volts, it typically can cut through metal up to approximately 1/2 inch (12.7 mm) thick, depending on the material and specific conditions.
2. Are 110V Plasma Cutters Any Good?
Yes, 110V plasma cutters can be quite good for certain applications. While they may not offer the same cutting capacity as higher voltage models, they are still highly useful for various tasks, particularly in settings where 220V power sources may not be readily available. Here are some advantages of 110V plasma cutters:
Portability: 110V plasma cutters are often more portable and easier to transport than their higher voltage counterparts. This makes them ideal for on-the-go cutting tasks or for use in locations where access to a 220V power source may be limited.
Versatility: While they may not cut through extremely thick materials like 220V models, 110V plasma cutters are still versatile tools that can handle a wide range of cutting tasks, including cutting thin sheets of metal, automotive repairs, HVAC work, and DIY projects.
Ease of Use: Many 110V plasma cutters are designed with user-friendly features, making them suitable for beginners or hobbyists who may not have extensive experience with cutting equipment.
Affordability: Generally, 110V plasma cutters tend to be more affordable than higher voltage models, making them accessible to a wider range of users.
Power Efficiency: For tasks that don’t require cutting through thick materials, a 110V plasma cutter can offer sufficient power while consuming less electricity compared to higher voltage models.
However, it’s important to note that 110V plasma cutters do have limitations in terms of cutting capacity, and they may not be suitable for heavy-duty industrial applications that require cutting through thick metal consistently. It’s essential to consider your specific cutting needs and the materials you’ll be working with when determining whether a 110V plasma cutter is the right choice for you.
3. How Much Power Am I Losing Buying A 110V Plasma Cutter?
Ans: When comparing a 110V plasma cutter to a higher voltage model, such as a 220V plasma cutter, there is a difference in power output. Generally, 220V plasma cutters have higher power output capabilities compared to 110V models. This means that you may experience some limitations in cutting capacity and speed with a 110V plasma cutter.
The amount of power loss you experience when using a 110V plasma cutter depends on several factors:
Cutting Capacity: 220V plasma cutters typically have higher cutting capacities than 110V models. If you frequently work with thicker materials that require more power to cut through, you may notice a significant difference in performance between the two types of plasma cutters.
Cutting Speed: Due to their lower power output, 110V plasma cutters may have slower cutting speeds compared to 220V models. This can result in longer cutting times for the same thickness of material.
Duty Cycle: The duty cycle of a plasma cutter refers to the amount of time it can operate continuously before needing to cool down. Lower voltage plasma cutters often have lower duty cycles compared to higher voltage models. This means you may need to take more frequent breaks during prolonged cutting sessions to prevent overheating.
Versatility: While 110V plasma cutters may be sufficient for many cutting tasks, they may not be as versatile as higher voltage models when it comes to cutting through a wide range of materials and thicknesses.
Power Efficiency: On the flip side, 110V plasma cutters tend to be more power-efficient compared to higher voltage models, which can result in lower energy costs over time.
Ultimately, the amount of power loss you experience when using a 110V plasma cutter depends on your specific cutting needs and the materials you work with. If you primarily work with thinner materials and value portability and convenience, a 110V plasma cutter may still be a suitable option despite the power limitations. However, if you require higher cutting capacities and faster cutting speeds, you may need to invest in a 220V plasma cutter for optimal performance.
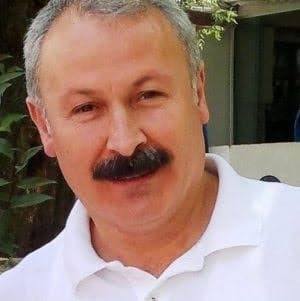
I’m Ivan D. Mitchell. I’m the Chief Engineer, Manufacturing Engineering Tool and Launch, specialising in automotive equipment design and build which meets World Class Manufacturing methodology. I have 15 years of work experience as a Tooling Specialist on some of the leading automotive manufacturing companies. When I launched this site, I wanted to create a platform where you’ll get everything about tools in one place. I also wanted to share my experience in the tool industry. I’ll do my best to share the information you need to truly make your tool using experience better. I hope you find our guides, reviews, information HELPFUL. If you have any inquiries, I’m always here to help you.